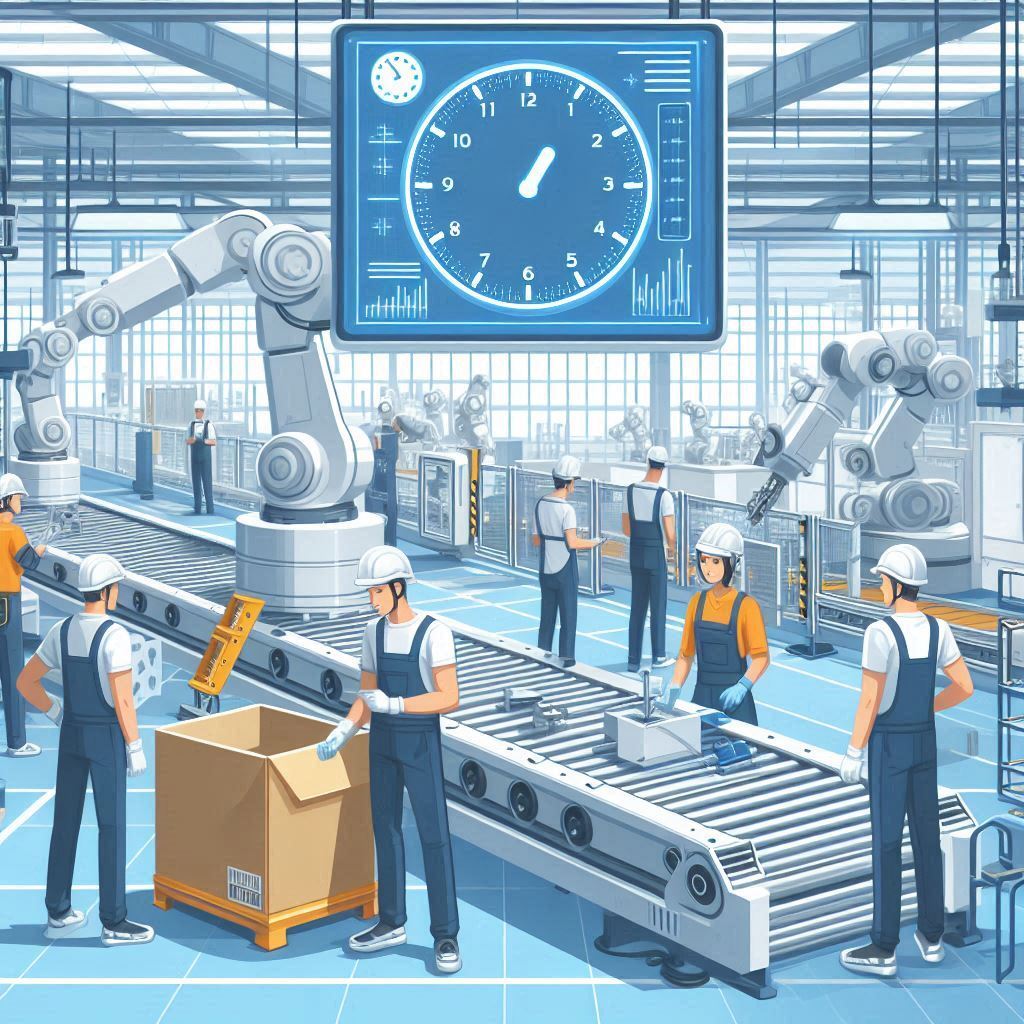
Key Challenges in Medium/High Volume Manufacturing
- Maintaining Consistent Quality
- Issue: Ensuring uniform quality across large production volumes is critical yet challenging, as defects can lead to significant waste and cost.
- Mitigation Strategy:
- Automated Quality Control: Implement automated quality control systems using sensors and AI to detect defects in real-time.
- Statistical Process Control (SPC): Use SPC techniques to monitor and control the production process, ensuring consistent quality.
- Equipment Downtime
- Issue: Unplanned equipment downtime can halt production lines, leading to delays and financial losses.
- Mitigation Strategy:
- Predictive Maintenance: Utilize predictive maintenance technologies to anticipate and address equipment failures before they occur.
- Redundant Systems: Implement redundant systems and backup equipment to minimize downtime.
- Supply Chain Complexity
- Issue: Managing a complex supply chain for high volume production can be challenging, with risks of delays, shortages, and variability in material quality.
- Mitigation Strategy:
- Supply Chain Visibility: Enhance visibility across the supply chain using digital tools like ERP and SCM (Supply Chain Management) software.
- Supplier Relationships: Develop strong relationships with reliable suppliers and diversify sourcing to mitigate risks.
- Inventory Management
- Issue: Balancing inventory levels to meet production demands without overstocking can be difficult and costly.
- Mitigation Strategy:
- Just-In-Time (JIT) Inventory: Implement JIT inventory practices to align material deliveries closely with production schedules.
- Inventory Optimization Tools: Use advanced analytics and inventory management tools to forecast demand and optimize stock levels.
- Labor Management
- Issue: Managing a large workforce and ensuring productivity while minimizing turnover and training costs is a significant challenge.
- Mitigation Strategy:
- Employee Training Programs: Develop comprehensive training programs to enhance skills and reduce onboarding time.
- Incentive Programs: Implement incentive programs to boost employee morale, productivity, and retention.
- Regulatory Compliance
- Issue: Ensuring compliance with industry regulations and standards can be complex and resource-intensive, especially in highly regulated industries.
- Mitigation Strategy:
- Compliance Management Systems: Use compliance management systems to track and ensure adherence to regulatory requirements.
- Regular Audits: Conduct regular internal audits to identify and address compliance issues proactively.
Mitigation Strategies: A Comprehensive Approach
- Lean Manufacturing Principles
- Implement lean manufacturing techniques to streamline operations, reduce waste, and improve overall efficiency. Techniques like value stream mapping and Kaizen can identify bottlenecks and enhance process flows.
- Advanced Manufacturing Technologies
- Automation: Invest in automation technologies such as robotics, automated guided vehicles (AGVs), and advanced machining systems to enhance precision, speed, and consistency.
- Industrial Internet of Things (IIoT): Leverage IIoT to connect machines and systems, enabling real-time monitoring, predictive maintenance, and enhanced decision-making.
- Digital Transformation
- Enterprise Resource Planning (ERP): Implement ERP systems to integrate and streamline various business processes, ensuring seamless coordination and efficiency.
- Manufacturing Execution Systems (MES): Use MES to track and document the transformation of raw materials into finished goods, ensuring traceability and process control.
- Flexible Manufacturing Systems
- Develop flexible manufacturing systems that can adapt to changes in product design and volume requirements without significant reconfiguration or downtime.
- Sustainability Practices
- Incorporate sustainability practices to reduce environmental impact and meet regulatory requirements. This includes energy-efficient processes, waste reduction, and recycling initiatives.
Case Study: Streamlining High Volume Production
Initial Challenges
A high volume automotive parts manufacturer faced issues with equipment downtime, inconsistent quality, and high inventory costs. The complex supply chain also led to frequent delays and material shortages.
Implemented Solutions
- Lean Manufacturing: The manufacturer adopted lean principles, including value stream mapping, to identify and eliminate waste in the production process.
- Automation and IIoT: Automated inspection systems and IIoT sensors were installed to monitor equipment health, predict maintenance needs, and ensure consistent quality.
- Supply Chain Management: Enhanced supply chain visibility using advanced SCM software, leading to better coordination with suppliers and reduced delays.
- Inventory Optimization: Implemented JIT inventory practices, reducing inventory costs by 20% and improving cash flow.
- Employee Training: Comprehensive training programs improved workforce skills and productivity, while incentive programs reduced turnover rates.
Results
The manufacturer saw a 30% reduction in downtime, a 25% improvement in product quality, and a 20% reduction in inventory costs. Enhanced supply chain coordination led to fewer production delays, and overall efficiency increased significantly.
Conclusion
Medium and high volume manufacturing presents distinct challenges, but with strategic approaches and advanced technologies, these can be effectively managed. Embracing lean principles, investing in automation and digital tools, optimizing supply chains, and focusing on workforce development are key to overcoming these challenges. By continuously improving and adapting to new technologies and market demands, manufacturers can maintain high efficiency, quality, and profitability in their operations.
Leave a Reply