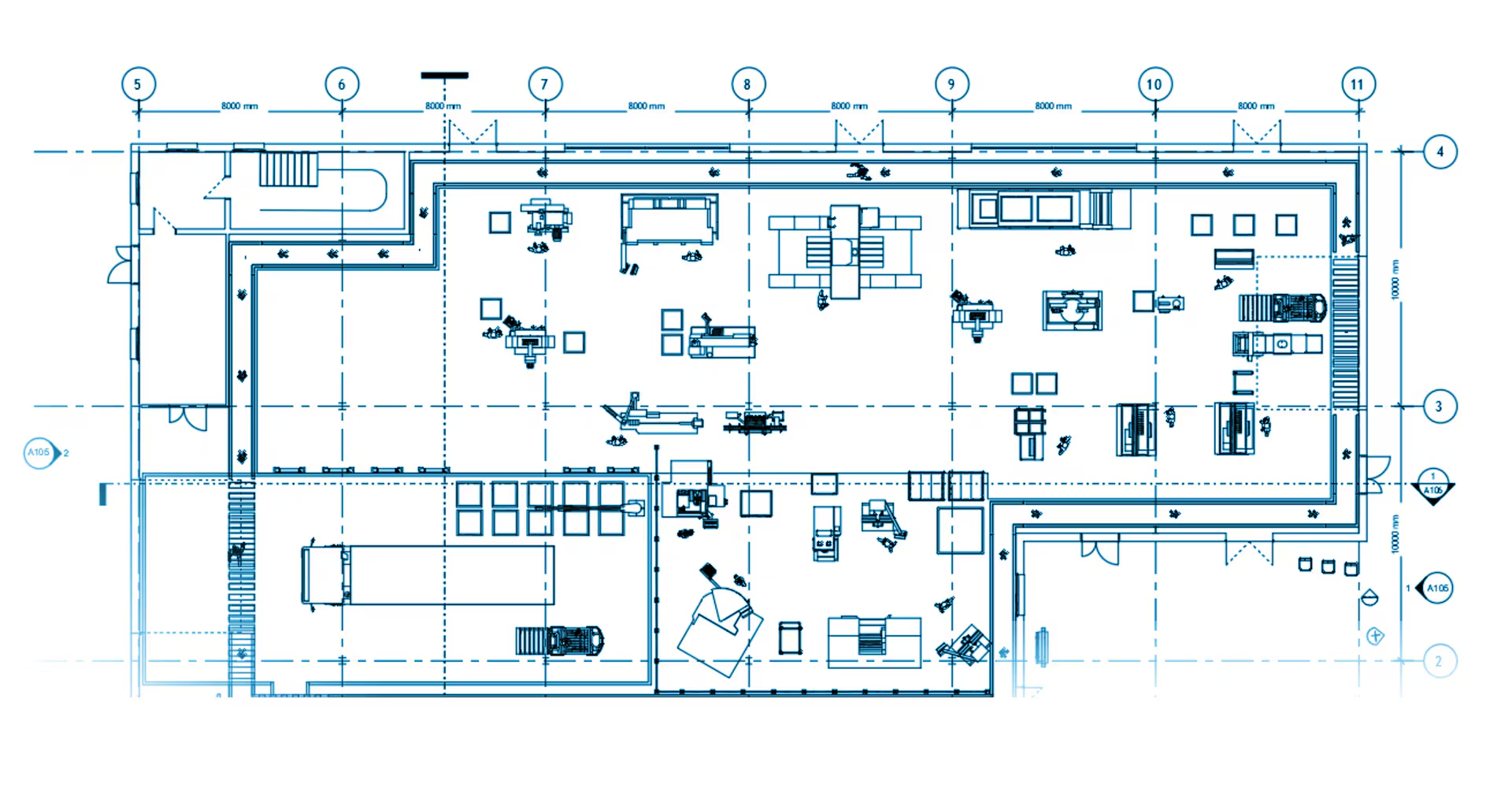
1. Work Cell Design and Space Allocation
Work Cells: Work cells are designed to streamline production processes by grouping machinery and tools required to complete a specific task or series of tasks.
Cellular Layouts: This layout arranges work cells in a manner that promotes efficient workflow and minimizes movement. Key principles include:
- Product-Focused Cells: Organize work cells around specific products or product families to reduce setup times and improve flow.
- U-Shaped Cells: Configure cells in a U-shape to minimize walking distances for operators and facilitate easy supervision and material handling.
Space Allocation for Work Cells:
- Activity Analysis: Conduct a detailed analysis of each activity within the work cell, including cycle times, operator movements, and tool usage. This helps in determining the exact space requirements.
- Ergonomic Considerations: Design work cells to minimize operator strain and fatigue. Ensure that tools and materials are within easy reach, and work surfaces are at appropriate heights.
- Flexibility and Scalability: Plan for flexibility in work cells to accommodate changes in production volume or product design. Use modular equipment that can be easily reconfigured.
2. Machinery and Equipment Placement
Machinery Layout: The placement of machinery is crucial for efficient space utilization and smooth workflow. Consider the following factors:
- Machine Size and Footprint: Measure the dimensions and operating space requirements of each machine, including maintenance and access areas.
- Process Flow: Arrange machines in the order of the production process to minimize material handling and transportation time. Linear or L-shaped layouts are common in sequential manufacturing processes.
- Inter-Machine Distances: Ensure adequate spacing between machines to allow for operator movement, maintenance access, and safety regulations.
Space Planning for Machinery:
- Capacity and Utilization: Analyze the capacity and utilization rates of each machine to determine the optimal number and placement of machines. Use simulation tools to model different scenarios and identify the best layout.
- Utility Connections: Plan for the placement of utilities such as electrical, water, and air supply lines. Ensure that these connections are accessible and do not obstruct workflows.
- Vibration and Noise Control: Consider the impact of machinery vibrations and noise on the surrounding work environment. Use isolation pads, barriers, and soundproofing materials where necessary.
Tooling and Storage Solutions
Tooling Management: Efficient management of tools and equipment is essential for minimizing downtime and ensuring smooth operations. Consider the following strategies:
- Tool Storage: Allocate space for tool storage close to the point of use. Use tool racks, cabinets, and shadow boards to organize tools systematically.
- Tool Access and Retrieval: Design storage solutions to facilitate quick access and retrieval. Implement Lean principles such as 5S (Sort, Set in Order, Shine, Standardize, Sustain) to maintain organization.
- Automated Tool Management: Consider automated tool management systems for larger facilities. These systems track tool usage, manage inventory, and reduce the time spent searching for tools.
Space Allocation for Tooling:
- Dedicated Tool Zones: Create dedicated zones for tool storage and maintenance. These zones should be easily accessible from all work cells and machinery.
- Space Optimization: Use vertical storage solutions and mobile tool carts to optimize floor space. Ensure that tool storage does not interfere with production activities.
- Maintenance and Calibration Areas: Allocate space for tool maintenance and calibration. These areas should be equipped with the necessary equipment and safety measures.
4. Analysis and Optimization Techniques
Workflow Analysis:
- Process Mapping: Create detailed process maps to visualize the flow of materials, information, and operators. Identify bottlenecks and areas of waste.
- Time and Motion Studies: Conduct time and motion studies to analyze the efficiency of current workflows and identify opportunities for improvement.
- Simulation Modeling: Use simulation software to model different layout scenarios and predict their impact on production efficiency. This helps in making data-driven decisions for space planning.
Optimization Strategies:
- Lean Manufacturing: Implement Lean principles such as JIT (Just-In-Time) production, Kanban systems, and continuous improvement to enhance workflow efficiency and reduce waste.
- Six Sigma: Use Six Sigma methodologies to identify and eliminate defects in the production process. This improves quality and reduces rework, which can impact facility design requirements.
- Continuous Improvement (Kaizen): Establish a culture of continuous improvement where employees are encouraged to suggest and implement layout and process improvements.
Conclusion
Effective space planning in manufacturing plants requires a comprehensive understanding of work cell design, machinery placement, tooling management, and the use of analysis and optimization techniques. By carefully considering these factors, industrial engineers can create plant layouts that maximize efficiency, reduce costs, and enhance overall productivity. Integrating Lean and Six Sigma principles, leveraging simulation tools, and fostering a culture of continuous improvement are essential for achieving optimal space utilization in manufacturing environments.
Leave a Reply