Welding Process Optimization: Enhancing Manufacturing Efficiency
In the realm of manufacturing, efficiency is the name of the game. Every step, every process, every technique must be optimized to ensure maximum output with minimal waste.
One area that often holds significant potential for improvement is welding.
In this blog post, I will delve into the importance of welding process optimization and how it can lead to significant enhancements in overall manufacturing efficiency.
WELDING PROCESS OPTIMIZATION
Welding is a fundamental process in many manufacturing industries, including automotive, aerospace, construction, and more. It involves joining materials together, typically metals, to create structures or components. Issues such as defects, distortion, and inefficiencies can arise if the process is not optimized.
By focusing on welding process optimization, manufacturers can address these challenges and unlock a host of benefits:
Improved Quality: Optimizing the welding process can lead to higher-quality welds with fewer defects. This, in turn, reduces the likelihood of rework or scrap, saving both time and money.
Increased Productivity: Efficiency improvements in welding can result in faster cycle times and increased throughput. This allows manufacturers to produce more parts in less time, ultimately boosting productivity.
Cost Reduction: Welding process optimization can lead to reduced material usage, lower energy usage, and decreased labor costs. These savings contribute to overall cost reduction and improved profitability.
Enhanced Safety: A well-optimized welding process minimizes the risk of accidents and injuries by implementing proper safety measures and controls.
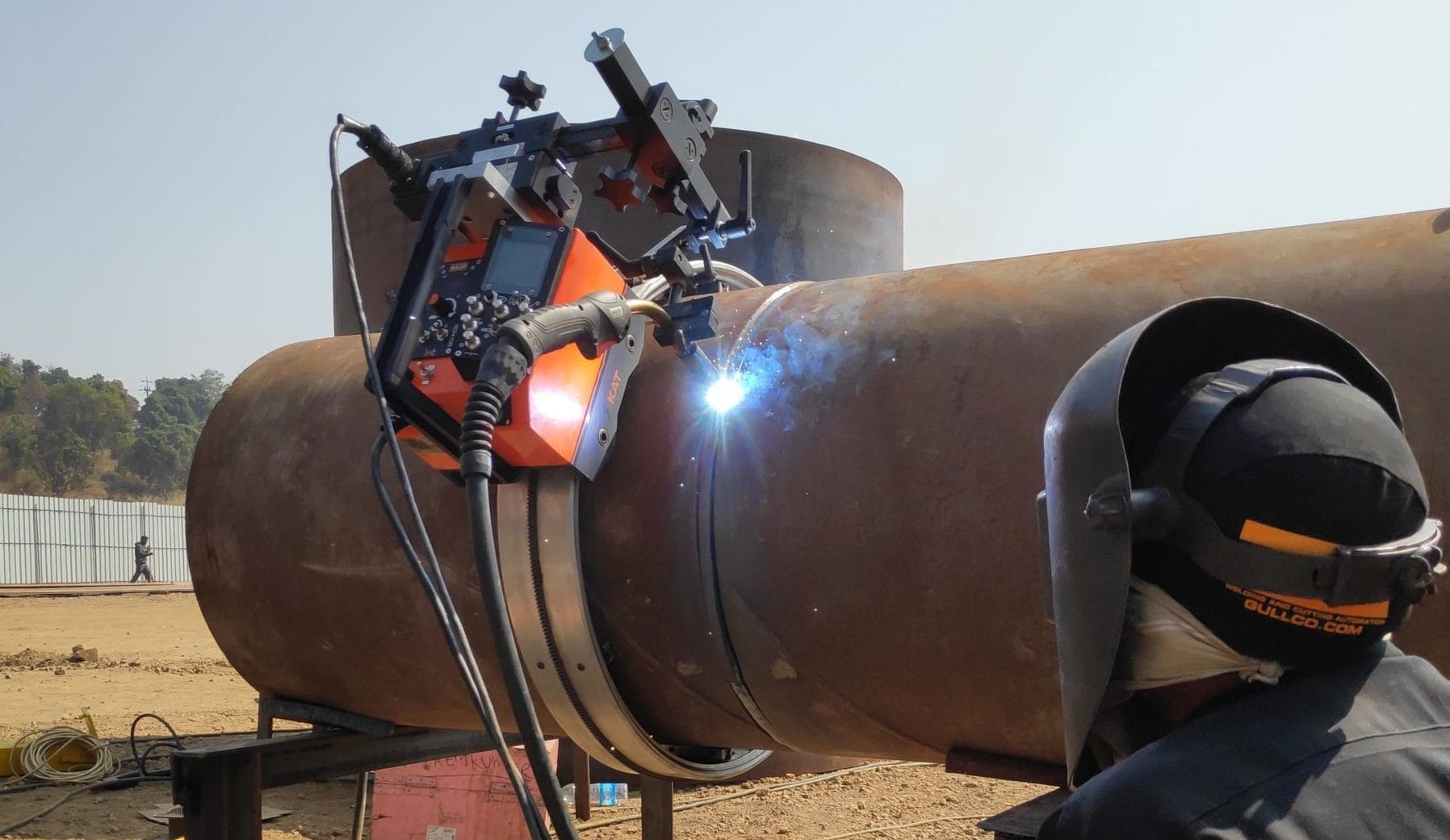
Strategies for Welding Process Optimization
Advanced Welding Techniques: Explore advanced welding techniques such as laser welding, electron beam welding, or friction stir welding, which offer advantages in terms of precision, speed, and quality.
Process Automation: Implement automated welding systems to increase productivity, reduce human error, and ensure consistent quality.
Workstation 5S: providing 5S for dedicated hose reels for oxy-acetylene, natural gas, compressed air can drastically reduce set-up times associated with the fabrication process.
Specialized Tools: sourcing specialized angle grinders or other tools for specific processes can drastically speed up production times and improve quality.
Conclusion:
By adopting advanced techniques, leveraging automation, and fostering a culture of continuous improvement, manufacturers can stay ahead of the competition and thrive in today’s fast-paced industrial landscape.
Leave a Reply