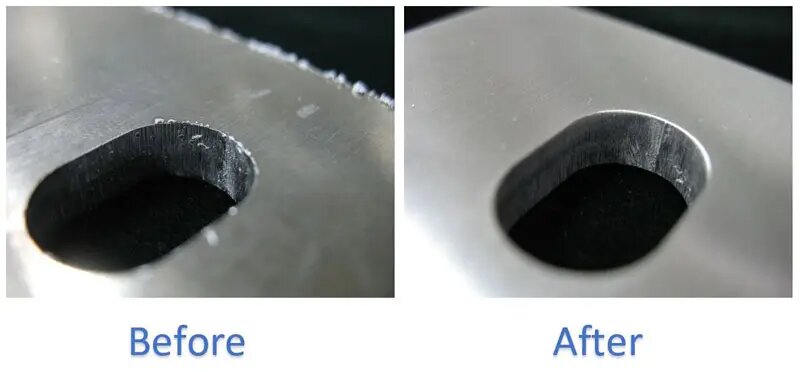
1. Manual Deburring
Manual deburring involves using hand tools such as files, sandpaper, or deburring knives to remove burrs. This method is typically used for small-scale production or intricate parts that require careful handling.
Applications:
- Prototyping and small-batch production.
- Custom parts with unique geometries.
- Finishing touches on precision components.
Advantages:
- High level of control and precision.
- Cost-effective for small quantities.
- Flexible and adaptable to different parts.
- Machine Deburring with a Tool
Machine deburring uses specialized tools mounted on machines to remove burrs. These tools can include rotary brushes, abrasive belts, or dedicated deburring tools on CNC machines.
Applications:
- High-volume production lines.
- Parts with consistent and repetitive burr patterns.
- Components requiring uniform finishes.
2. Machine Deburring
Machine deburring uses specialized tools mounted on machines to remove burrs. These tools can include rotary brushes, abrasive belts, or dedicated deburring tools on CNC machines. Other common methods include tumbling, sanding, and grinding.
Applications:
- High-volume production lines.
- Parts with consistent and repetitive burr patterns.
- Components requiring uniform finishes.
Advantages:
- High efficiency and consistency.
- Suitable for integration into automated production lines.
- Reduces manual labor and increases throughput.
3. Chemical Deburring
Chemical deburring, also known as chem milling, uses a controlled chemical solution to dissolve burrs on metal parts. This deburr method is particularly effective for removing burrs from complex geometries that are difficult to reach with mechanical methods.
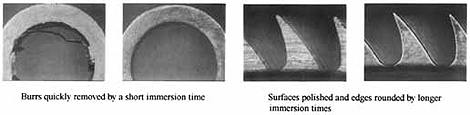
Applications:
- Precision parts in the aerospace and automotive industries.
- Medical instruments and implants.
- Electronic components.
- STI offers various Deburr products to achieve chemical deburring. Check them out here!
Advantages:
- Ideal for complex shapes.
- Does not alter the part’s structural integrity.
- Can be automated for high-volume production.
4. Electrolytic Deburring (Electropolishing)
Electrolytic deburring, commonly known as electropolishing, uses an electrochemical process to remove burrs and improve the surface finish of metal parts. The part is submerged in an electrolyte solution and connected to an electrical current, which dissolves the burrs and smoothens the surface.
Applications:
- Stainless steel parts used in food and pharmaceutical industries.
- Medical devices requiring a high degree of smoothness.
- Aerospace components where surface integrity is crucial.
Advantages:
- Provides a high-quality, smooth finish.
- Removes burrs and improves corrosion resistance.
- Suitable for intricate and delicate parts.
5. Thermal Deburring
Thermal deburring, also known as thermal energy method (TEM) deburring, involves exposing the part to a controlled explosion of gas. The rapid increase in temperature burns off the burrs without damaging the part itself.
Applications:
- Precision machined parts with internal passages.
- Parts used in hydraulic systems.
- Automotive fuel injection components.
Advantages:
- Removes internal and external burrs simultaneously.
- Efficient for parts with complex geometries.
- Fast and effective for high-volume production.
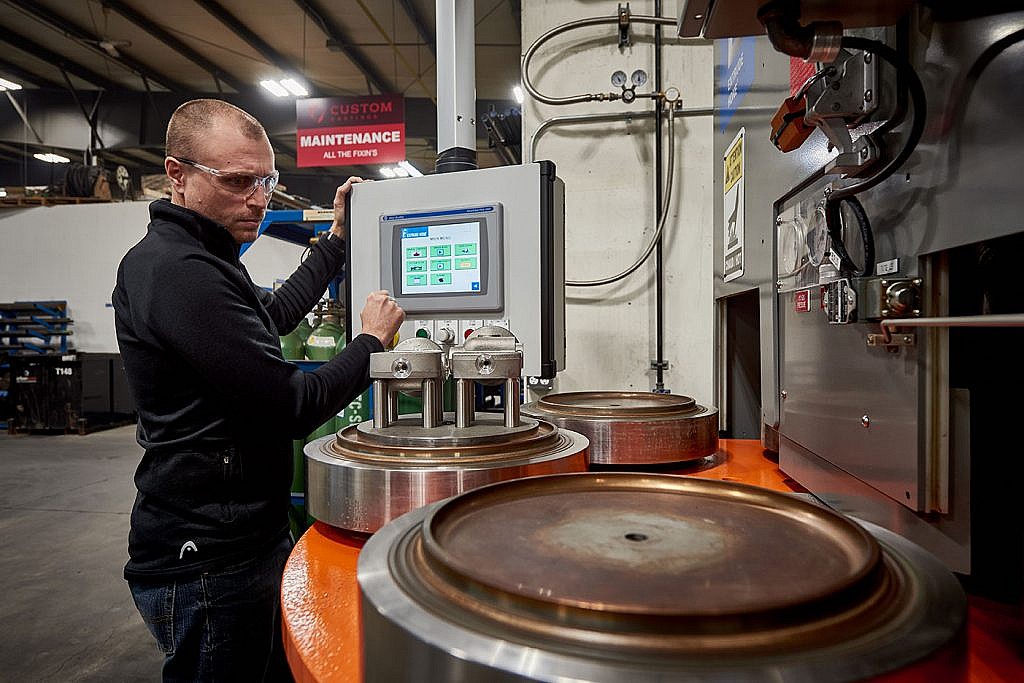
6. Vibratory Finishing
Vibratory finishing involves placing parts in a vibrating bowl filled with abrasive media. The constant vibration causes the abrasive media to rub against the parts, removing burrs and polishing surfaces.
Applications:
- Mass finishing of small parts.
- Deburring and polishing of jewelry.
- Finishing parts used in consumer electronics.
Advantages:
- Suitable for bulk processing.
- Can achieve uniform finishes on multiple parts.
- Adjustable for different materials and finishes.
7. Ultrasonic Deburring
Ultrasonic deburring uses high-frequency sound waves to create cavitation bubbles in a liquid medium. When these bubbles collapse, they generate localized high pressure that removes burrs.
Applications:
- Delicate or intricate parts.
- Precision components in the aerospace and medical industries.
- Micro-machined parts.
Advantages:
- Non-contact method, ideal for delicate parts.
- Can reach difficult-to-access areas.
- Environmentally friendly process.
Choosing the Right Deburr Method
The choice of deburring method depends on several factors, including the material of the part, the complexity of its geometry, the size and location of the burrs, and the desired surface finish. For instance, chemical and electrolytic deburring are ideal for complex, delicate parts requiring a high-quality finish, while thermal and mechanical methods are better suited for robust, high-volume applications.
Conclusion
Deburring is a critical step in manufacturing that ensures parts meet the required specifications for functionality, safety, and aesthetics. By understanding the various deburring techniques available—manual deburring, machine deburring, chemical deburring, electrolytic deburring, thermal deburring, mechanical deburring, vibratory finishing, and ultrasonic deburring—manufacturers can select the most appropriate method for their specific needs, enhancing the quality and performance of their products.
Leave a Reply