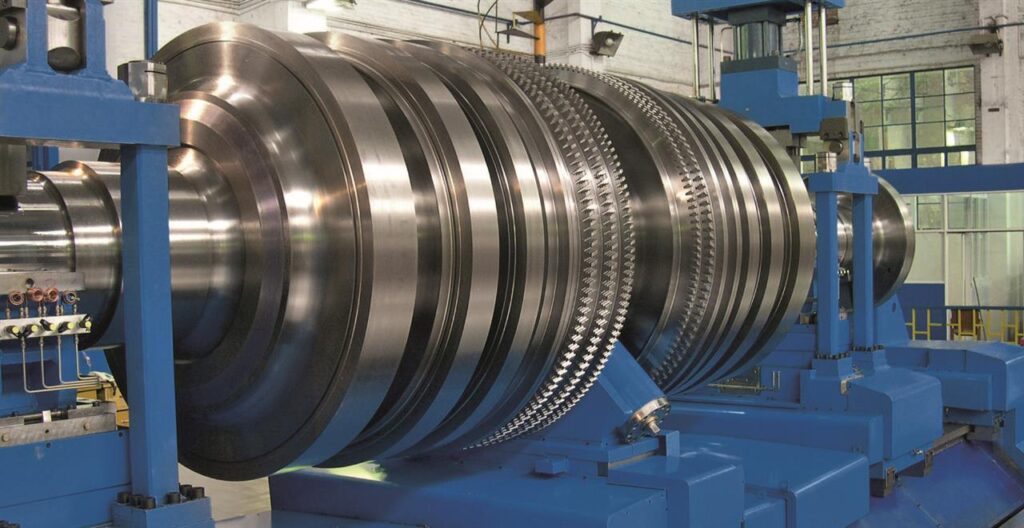
Rough Machining:
- Start with the raw material input, specifying the type and quantity of material required for rough machining.
- Document the rough machining process, including the setup of the machine, tool selection, cutting parameters, and the actual machining operations.
- Note any quality checks or inspections performed during rough machining to ensure dimensional accuracy and surface finish.
Finish Machining:
- Transition from rough machining to finish machining, outlining the steps involved in refining the workpiece to meet final specifications.
- Detail the setup and tooling for finish machining, including any adjustments made to optimize surface finish and tolerances.
- Document any secondary operations such as threading, drilling, or milling that may be required to achieve the desired geometry.
Deburring:
- After finish machining, move on to the deburring process to remove burrs, sharp edges, and surface imperfections.
- Specify the deburring methods employed, whether manual or automated, and detail the equipment and tools used for this task.
- Include any post-deburring inspections to ensure the workpiece meets quality standards before proceeding to the next stage.
Level of Detail in Process Mapping
When it comes to process mapping a machining workflow, the level of detail should strike a balance between clarity and practicality. Here are some guidelines to consider:
- Focus on Key Steps: Highlight the critical processes and decision points that have a significant impact on product quality, lead time, or cost.
- Include Inputs and Outputs: Clearly define the inputs required for each process (e.g., raw materials, tooling) and the expected outputs (e.g., machined components, scrap).
- Document Variability: Acknowledge variations in process parameters, material properties, and environmental factors that may influence workflow performance.
- Avoid Overcomplication: While detail is essential, avoid overwhelming the map with unnecessary complexity. Stick to the essential information needed to understand and improve the workflow.
By following these principles, process mapping becomes a powerful tool for optimizing machining processes, driving efficiency, and delivering high-quality products consistently. With a clear understanding of the rough machining, finish machining, and deburring processes, manufacturers can identify opportunities for streamlining operations, reducing waste, and enhancing overall productivity.
Common Machining Improvements
After process mapping a machining workflow, many wastes and opportunities should be readily apparent and identified. Some of the most common improvements found include:
- Specialized Deburr Tools: Creating special tools to speed up the deburr process. If deburr is done manually on a part, this is a good potential solution.
- Tool Availability 5S: Utilizing advanced tool management systems to optimize tool usage, track tool life, automate tool changes, and ensure the availability of the right tool for each machining operation, thus improving efficiency and reducing tool-related downtime.
- Set-Up Fixtures: Designing efficient machining setup fixtures can significantly reduce setup times, ensuring quick and precise alignment of the part for machining processes. Allows for probing of a part compared to manual measurements.
- Predictive Maintenance: Ensuring adequate preventative maintenance plans are implemented can drastically reduce machine downtimes in the process. This includes having maintenance plans, spare parts inventory, and a maintenance log.
Leave a Reply