WHAT ARE THE 7 WASTES OF MANUFACTURING?
Welcome to our overview on the 7 Wastes of Lean. Join us as we delve into each of these wastes, uncovering practical strategies to eliminate inefficiencies and optimize your processes.
WHY DO WE CARE ABOUT THE 7 WASTES?
By understanding and addressing these wastes, businesses can streamline operations, enhance value for customers, and achieve sustainable continual growth.
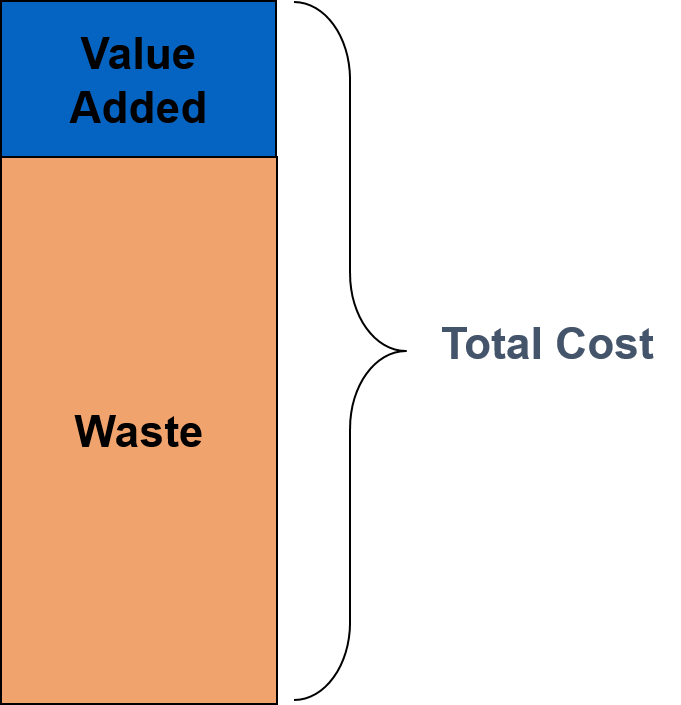
VALUE-ADDED (VA) / NON-VALUE ADDED (NVA)
Value-Added Activities directly contribute to customer value/needs, while Non-Value Added often represent the 7 Wastes. Identifying and eliminating Non-Value Added Activities helps streamline processes and reduce these wastes.
T.I.M.W.O.O.D.
AN EASY ACRONYM TO REMEMBER YOUR WASTES
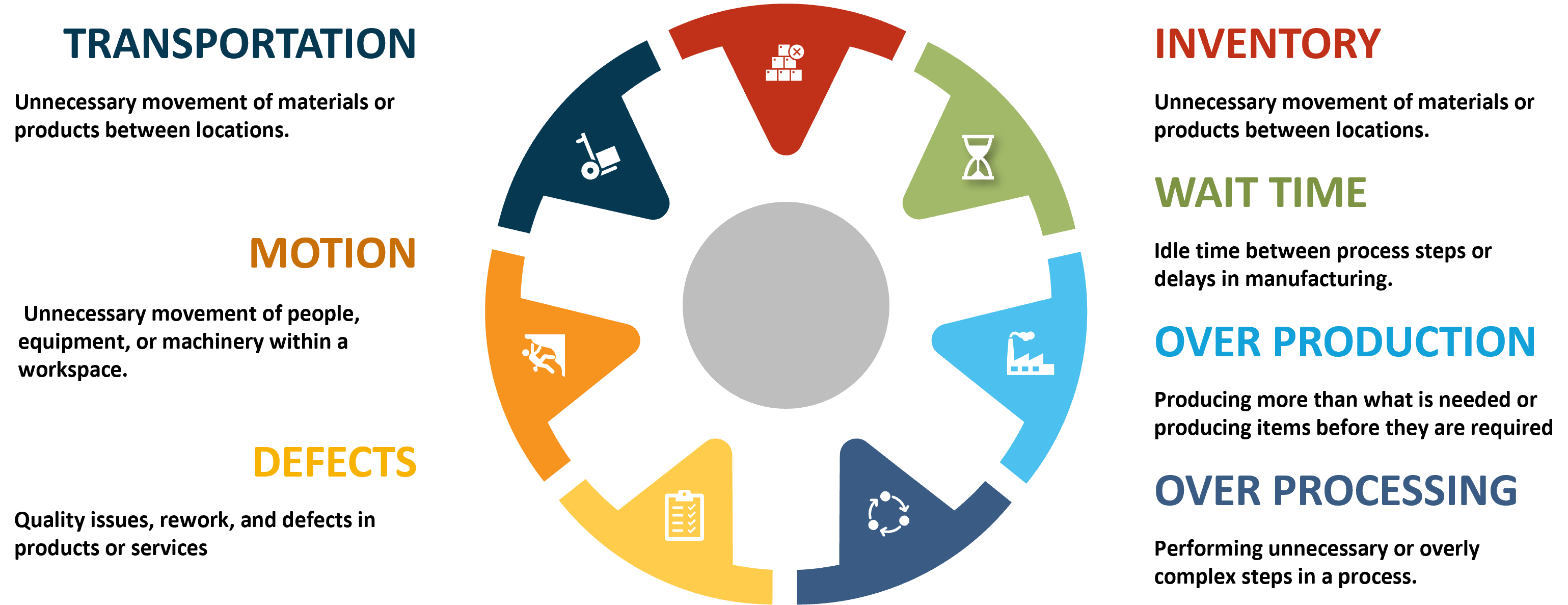
WHAT IS THE WORST WASTE?
OVER PRODUCTION
Often considered the most detrimental of the seven production wastes, occurs when goods are manufactured in excess of demand.
Over Production masks all of the wastes within it, and also amplifies the other 6 wastes when we over-produce a product.
HOW DO WE ELIMINATE THESE WASTES?
Industrial Engineers can utilize systematic approaches, like DMAIC and Process Maps, to identifying and eliminating waste, optimizing processes, and enhancing overall efficiency within lean manufacturing environments.