Mastering SMED: Speeding Up Changeovers in Manufacturing
Single Minute Exchange of Dies (SMED) is a lean manufacturing methodology aimed at reducing the time it takes to switch from one process to another. While Dies are not used in every process, this concept still applies to many work environments. The goal of SMED is to perform changeovers in the shortest time possible and reduce the setup times associated.
SMED involves several key principles which we will explore in this blog post:
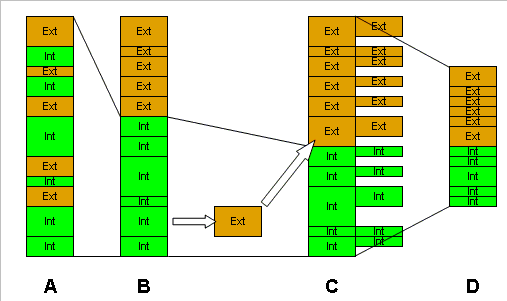
Conclusion:
SMED is a game-changer in the world of manufacturing. By reducing setup times, you can enhance efficiency, cut costs, and improve product quality. Sure, it takes some effort to get started, but the rewards are well worth it. Plus, you can dive into other lean methodologies like Kaizen, Value Stream Mapping, and DMAIC to keep the improvements rolling.
Leave a Reply