Key Challenges in Low Volume Manufacturing
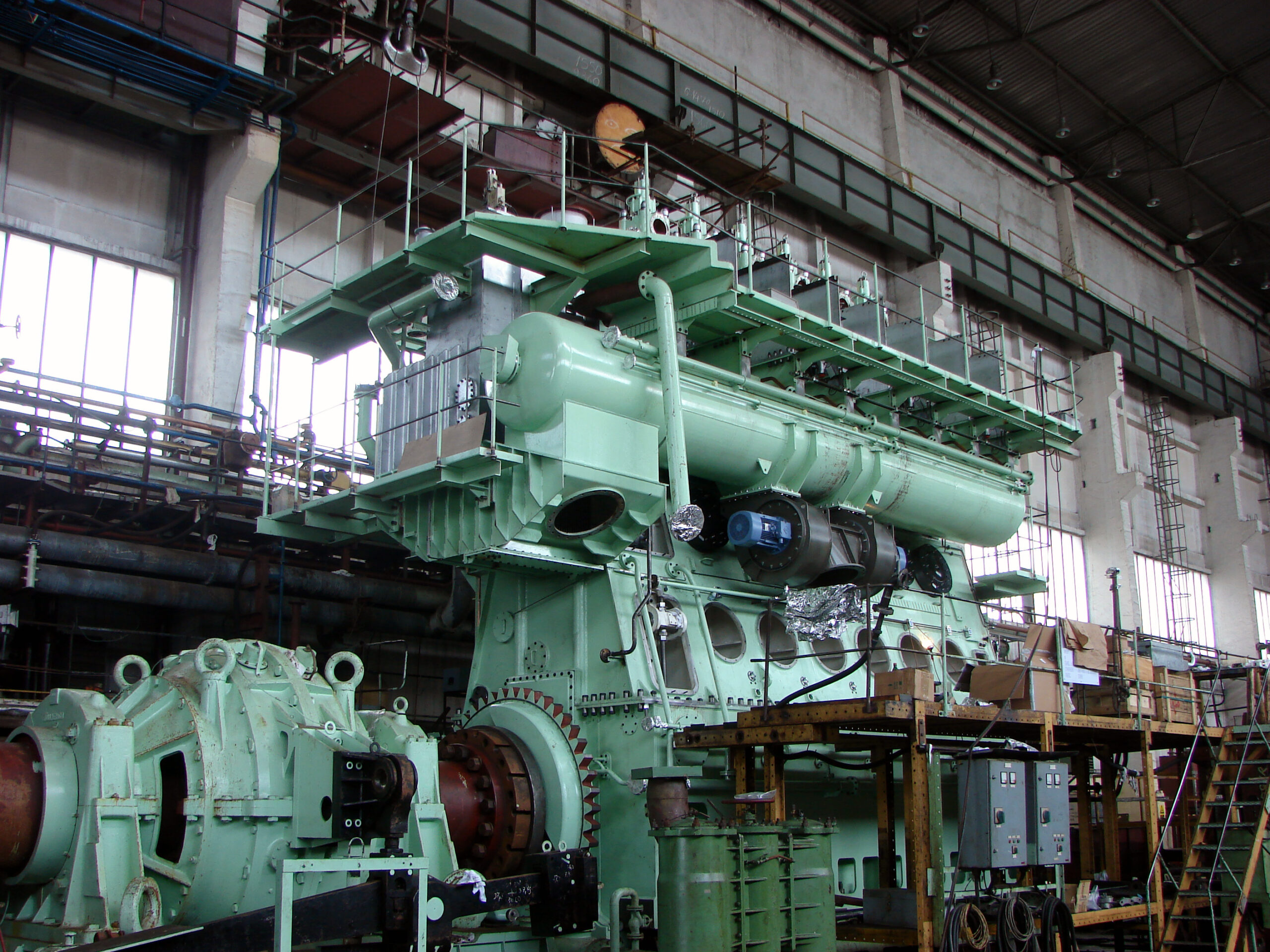
- High Production Costs
- Issue: Producing small batches of products often incurs higher per-unit costs compared to mass production. Fixed costs such as setup, tooling, and machine calibration are spread over fewer units, driving up the cost per unit.
- Mitigation Strategy:
- Flexible Manufacturing Systems: Invest in flexible and reconfigurable manufacturing systems that can quickly switch between different tasks and product lines without extensive retooling.
- Batch Scheduling: Optimize production schedules to group similar products and reduce the frequency of changeovers.
- Inventory Management
- Issue: Managing inventory for low volume production can be tricky, as holding too much stock ties up capital and increases storage costs, while holding too little risks production delays.
- Mitigation Strategy:
- Just-In-Time (JIT) Inventory: Adopt a JIT inventory system to align raw material deliveries with production schedules, reducing the need for large inventories.
- Vendor-Managed Inventory (VMI): Collaborate with suppliers to manage inventory levels, ensuring timely replenishment without overstocking.
- Quality Control
- Issue: Ensuring consistent quality in small batch production is challenging, especially when processes and setups frequently change.
- Mitigation Strategy:
- Standard Operating Procedures (SOPs): Develop and adhere to strict SOPs to maintain quality standards across different batches.
- Inline Quality Checks: Implement quality checks at various stages of production to catch defects early and reduce rework costs.
- Skilled Labor Shortage
- Issue: Finding and retaining skilled workers for specialized tasks in low volume manufacturing can be difficult, especially when the work is not continuous.
- Mitigation Strategy:
- Cross-Training Employees: Train employees to perform multiple roles, increasing workforce flexibility and ensuring that production can continue smoothly despite labor shortages.
- Continuous Learning: Offer ongoing training and development opportunities to enhance employee skills and reduce turnover.
- Supply Chain Variability
- Issue: Low volume manufacturers often face variability in their supply chains, leading to delays and disruptions that can halt production.
- Mitigation Strategy:
- Supplier Diversification: Develop relationships with multiple suppliers to reduce dependency on any single source and ensure a steady flow of materials.
- Local Sourcing: Whenever possible, source materials from local suppliers to reduce lead times and transportation risks.
- Technological Investment
- Issue: Investing in advanced manufacturing technologies can be cost-prohibitive for low volume operations, yet necessary to maintain competitiveness.
- Mitigation Strategy:
- Incremental Investment: Start with smaller, scalable technology investments that can grow with your production needs.
- Leasing Equipment: Consider leasing equipment to spread out the costs and remain flexible in adapting to new technologies.
Mitigation Strategies: A Comprehensive Approach
- Lean Manufacturing Principles
- Embrace lean manufacturing to identify and eliminate waste, improve efficiency, and reduce costs. Techniques such as 5S (Sort, Set in order, Shine, Standardize, Sustain) and Kaizen (continuous improvement) can be particularly beneficial.
- Advanced Manufacturing Techniques
- Leverage advanced manufacturing techniques such as additive manufacturing (3D printing), which allows for rapid prototyping and production of complex parts without the need for expensive tooling.
- Collaborative Partnerships
- Foster strong relationships with key suppliers and partners. Collaboration can lead to shared resources, better pricing, and more reliable supply chains.
- Digital Transformation
- Implement digital tools and software to enhance planning, monitoring, and control of the manufacturing process. Enterprise Resource Planning (ERP) systems and Manufacturing Execution Systems (MES) can provide real-time insights and improve decision-making.
- Customization and Value-Added Services
- Offer customization and value-added services to justify higher prices and differentiate from competitors. Focus on delivering unique features, high quality, and exceptional customer service.
Conclusion
While low volume manufacturing presents several challenges, these can be effectively managed with the right strategies and tools. By embracing lean principles, investing in flexible technologies, enhancing workforce skills, and fostering strong supplier relationships, manufacturers can navigate the complexities of low volume production. The key lies in continuous improvement, adaptability, and a commitment to quality, ensuring that low volume manufacturing remains a viable and profitable business model in today’s dynamic market.
Leave a Reply