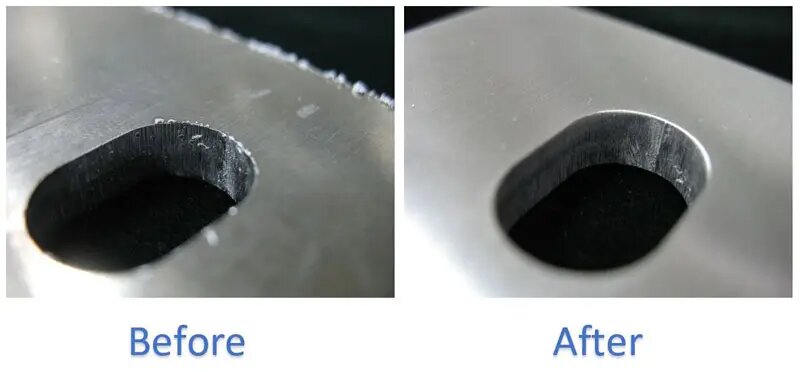
What is DEBURR 1000TM?
DEBURR 1000TM represents a paradigm shift in deburring technology. It leverages a chemical process devoid of electricity, efficiently removing burrs caused by cutting, milling, forging, and molding from steel parts. Unlike mechanical methods, DEBURR 1000TM eliminates burrs at their base, dissolving them entirely in the process bath. This approach ensures even the most intricate parts retain their shape and integrity.
Required Equipment
Tank Requirements: The tanks for Deburr 1000TM should be constructed of standard polypropylene. Welded is acceptable, but seamless is preferable. The shape of this tank is not critical; a plain square or rectangular shape is sufficient.
Cooling Apparatus: Deburr 1000TM tanks must be equipped with a 300 series stainless steel or PTFE cooling coil that will be connected to a suitable chiller capable of removing the heat generated by the exothermic deburring reaction and maintaining a constant operating temperature to +/- 1.0°C.
Filtration: A filtration system utilizing a 10-micron or finer bag or cartridge is recommended. The wetted parts of this filter system must only be 300 series stainless steel, polypropylene, CPVA, PTFE, Viton or Silicone. The flow from the filtration system should not be directed at the work pieces in the tank.
Agitation: No agitation of the bath is required, although rotation or movement of the work pieces may be desirable.
Incompatible Materials: Specific materials that cannot come in contact with the bath are glass, aluminum, lead, copper, brass, bronze, chlorides, or calcium.
Deburr Procedures
The procedure for deburring steel parts with DEBURR 1000 is:
- Steel soak cleaner, 160-190ºF, 10 minutes
- Rinse
- Pickling in H2SO4 based solution, ambient to 45ºC, 1-2 minutes
- Rinse
- Deburr 1000TM bath (30 seconds to 5 minutes)
- Rinse
- Pickling, ambient to 40ºC, 30 seconds
- Rinse
- Ultrasonic cleaning, 1 minute
- Rinse
- Rust inhibitor or subsequent metal finishing process
The following parameter ranges are recommended for the Deburr 1000TM bath:
TEMPERATURE 15-17ºC
CONCENTRATION 160-170 ml/l H2O2 35%
pH 3.7-4.0
LOADING 1 dm2/l or 0.4 ft2/gal
ROTATION 1-10 RPM or mild agitation of solution and/or workpieces
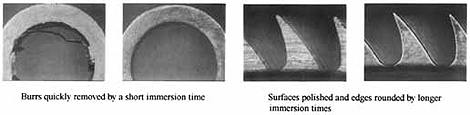
The DEBURR 1000TM process will not damage sensitive surfaces as with many tumbling and grinding operations.
Longer immersion times in Deburr 1000TM may be used to polish, shape, and round the edges of precision parts. Surfaces can be polished to a peak to valley height of 0.1 micron.
Achieving these outstanding surface characteristics has proven especially useful for moving parts in the textile, gear, molding, and many other high-speed assembly and processing industries where precision metal parts contact other metal parts or delicate materials. Smoother and rounder surfaces on these parts provide greater reliability, quieter operations, longer life for the deburred parts and less damage to parts and materials that come in contact with the deburred parts.
SURFACE TECHNOLOGY, INC.
Ready to improve your deburr process? Reach out to Surface Technology Inc for more information on their DEBURR 1000TM Chemical Deburr Solution and Product.
Leave a Reply