SET IN ORDER 5S
This phase aims to minimize waste by ensuring everything has a designated place, streamlining processes, and enhancing workplace safety. During the Set in Order Phase of 5S, items are organized systematically for optimal workflow and efficiency.
Tasks typically include assigning specific locations for tools and materials, labeling storage areas clearly, and establishing standard procedures for item placement and retrieval.
SET IN ORDER GUIDELINES
– If items are used together, they should be stored together
– Arrange tools and material by frequency used, with higher items closest to the Point of Use/User
– Devise a “let-go” system with retractable cord attached, so tools are automatically stored.
Place items so they can be easily accessed without bending, moving, twisting, etc.
SET IN ORDER STRATEGIES
LABELS AND SIGNS
Labeling tool boxes, drawers, individual tools and posting standardized signs drives quick visual identification. 5S Labeling and Signage makes it simple for unfamiliar and familiar operators to locate items and store them appropriately.
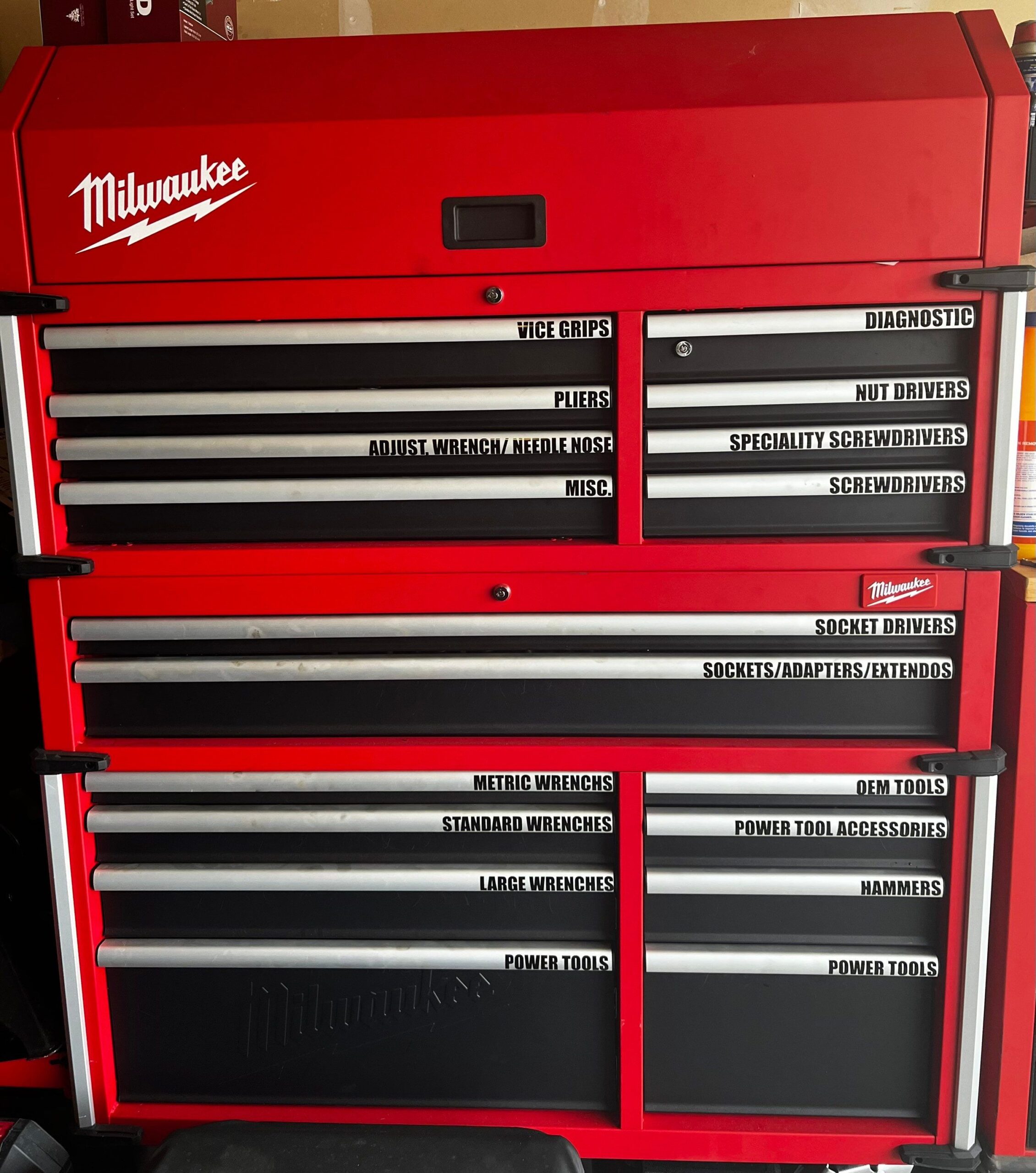
LINE MARKING
Tape or Paint Markings are applied to designated areas around the factory. The purpose is to create a standardized format for coloring and area designation. By marking the boundaries of these areas, teams and visitors can make sense of the production space.
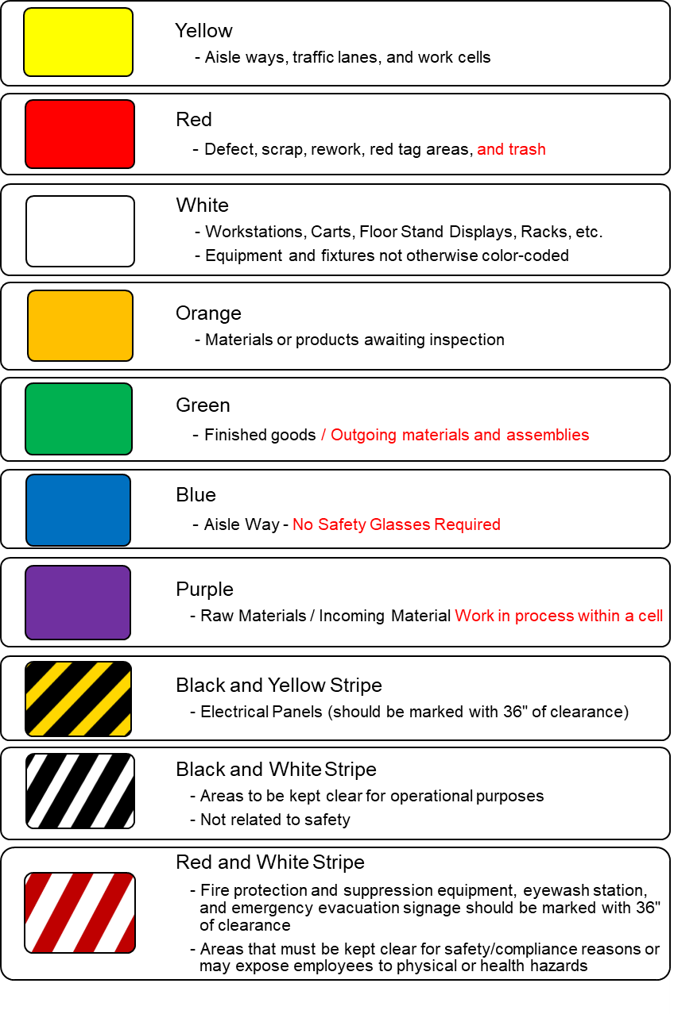
TOOL OUTLINE / SHADOW FOAM
Tool Outlining or Shadow Foams are applied to toolboxes or other storage methods around the factory. The purpose is to create a standardized “home” for each tool with a set place. By defining and marking these areas with Shadow Foam Boards, tools can easily be identified as missing or out of place.

PHASES
Click each Step below to learn more about the 5S Process.
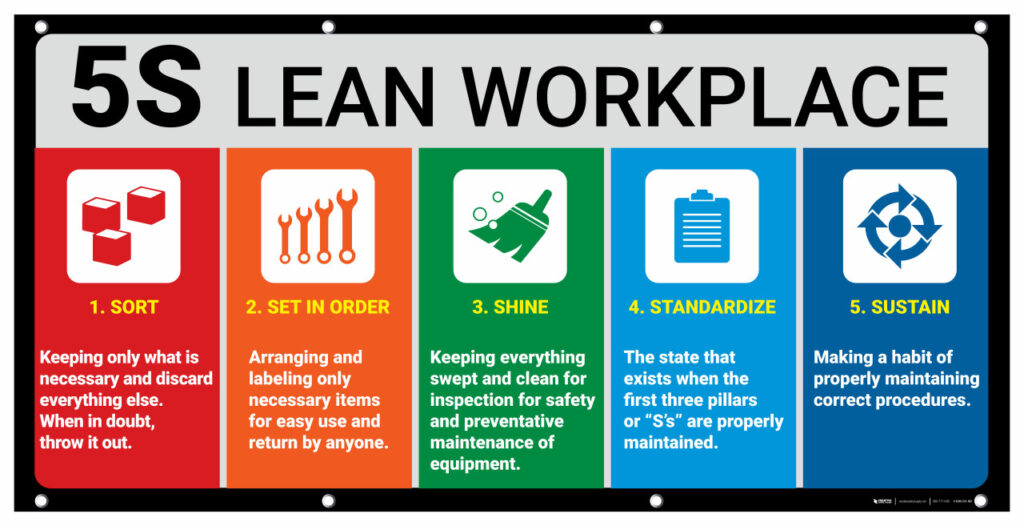