SORT 5S
The cornerstone of 5S. During the Sort Phase of 5S, items are systematically evaluated to determine their necessity in the workspace. Unnecessary items are removed or relocated. By decluttering and removing items that are not needed, the workspace becomes more streamlined and efficient, fostering a safer and more productive environment.
SORT ELIMINATES:
– Tools and materials that impede or inhibit workflow
– Wait Times or Lost Time looking for parts, tools, materials, etc.
– Large stockpiles of material or excess inventory
– Safety Hazards associated with clutter and disorganization
GOALS OF SORT
RED TAGS
To assist in the Sort Phase we use a tool known as Red Tags. They help you identify objects that need to be removed from the workplace. Red Tags clue everyone to an item or area that needs attention.
TAG INFO:
Indicate which action should be taken:
Leave the Item
Relocate the Item
Dispose of the Item
Recycle the Item
Place in “Red Tag Holding Area”
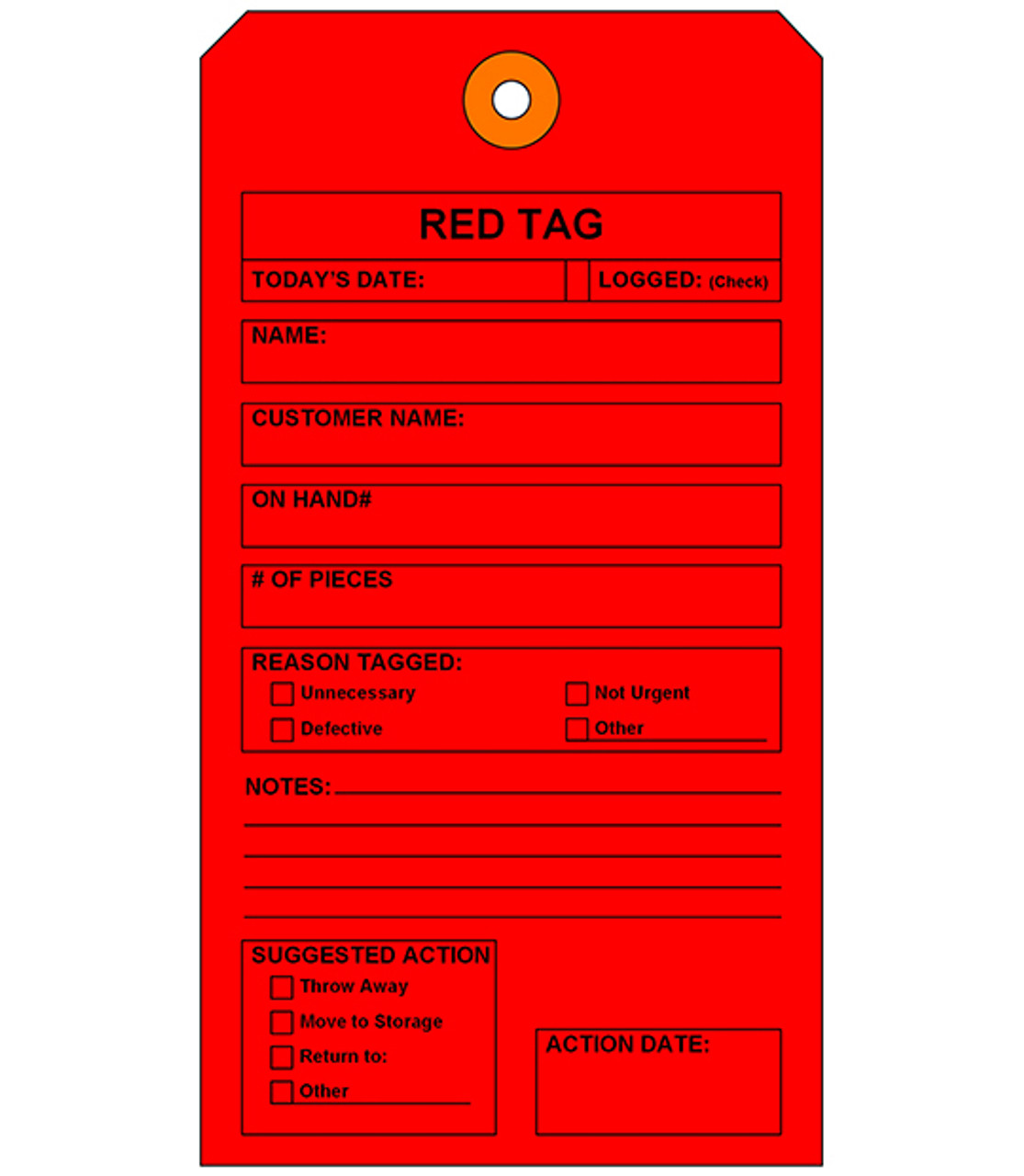
Red Tag Holding Area
The Red Tag Holding Area is a location where items are placed temporarily while their value and future state is determined.
PHASES
Click each Step below to learn more about the 5S Process.
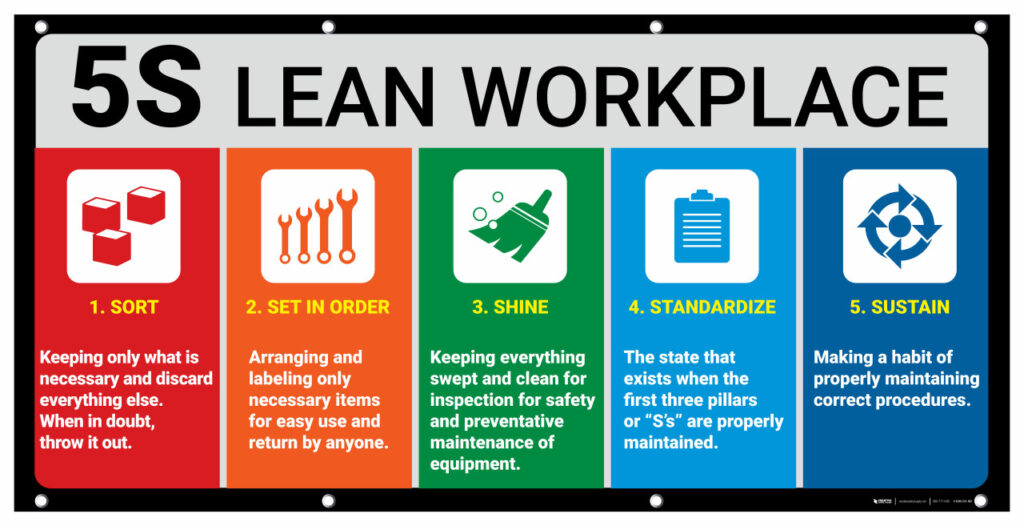