Understanding the Bottlenecks
The first step in reducing wait times is identifying bottlenecks in the production process. Bottlenecks are points in the workflow where delays occur, causing a ripple effect that slows down the entire operation. Common bottlenecks in engine manufacturing may include:
- Material Handling Delays: Time lost in moving materials between stages.
- Machine Downtime: Periods when machines are not operational due to maintenance or setup.
- Quality Control Delays: Time taken for thorough inspection and rework of faulty parts.
- Supply Chain Interruptions: Delays in receiving necessary components from suppliers.
Strategies for Reducing Wait Times
- Implement Lean Manufacturing PrinciplesLean manufacturing focuses on minimizing waste without sacrificing productivity. Key lean principles include:
- 5S Methodology: Sort, Set in order, Shine, Standardize, and Sustain. This approach organizes the workplace, reduces clutter, and streamlines processes.
- Value Stream Mapping (VSM): A visual tool that maps out all steps in the production process to identify and eliminate non-value-added activities.
- Continuous Improvement (Kaizen): Encouraging small, incremental changes to improve efficiency and reduce wait times continuously.
- Optimize Layout and Workflow
- Cellular Manufacturing: Grouping machines and processes based on similar functions to reduce transportation time and improve workflow efficiency.
- Just-In-Time (JIT) Production: produce components as needed rather than in advance, reduce inventory costs and wait times.
- Invest in Advanced Technologies
- Automation: Utilizing automated systems for repetitive tasks can significantly reduce wait times and improve consistency. Robots and CNC machines can enhance precision and speed in engine assembly.
- Industrial Internet of Things (IIoT): Connecting machines and systems via the internet to collect real-time data can help predict maintenance needs, reducing unexpected downtime.
- Enhance Workforce Training and Engagement
- Cross-Training Employees: Training workers to perform multiple tasks increases flexibility and ensures that operations continue smoothly even if one worker is absent.
- Employee Involvement: Engaging employees in identifying inefficiencies and suggesting improvements can lead to innovative solutions and increased buy-in for new processes.
- Implement Robust Quality Control Measures
- Inline Quality Checks: Incorporating quality checks at various stages of the production process to catch defects early and reduce rework time.
- Predictive Maintenance: Using data analytics to predict when machines will need maintenance can prevent unexpected breakdowns and reduce downtime.
- Improve Supply Chain Management
- Supplier Collaboration: Working closely with suppliers to ensure timely delivery of high-quality components.
- Inventory Management: Implementing inventory management systems to track stock levels and automate reordering processes.
Case Study: Reducing Build Times for Engines
Let’s consider a low volume engine manufacturing plant that successfully reduced build times by implementing these strategies.
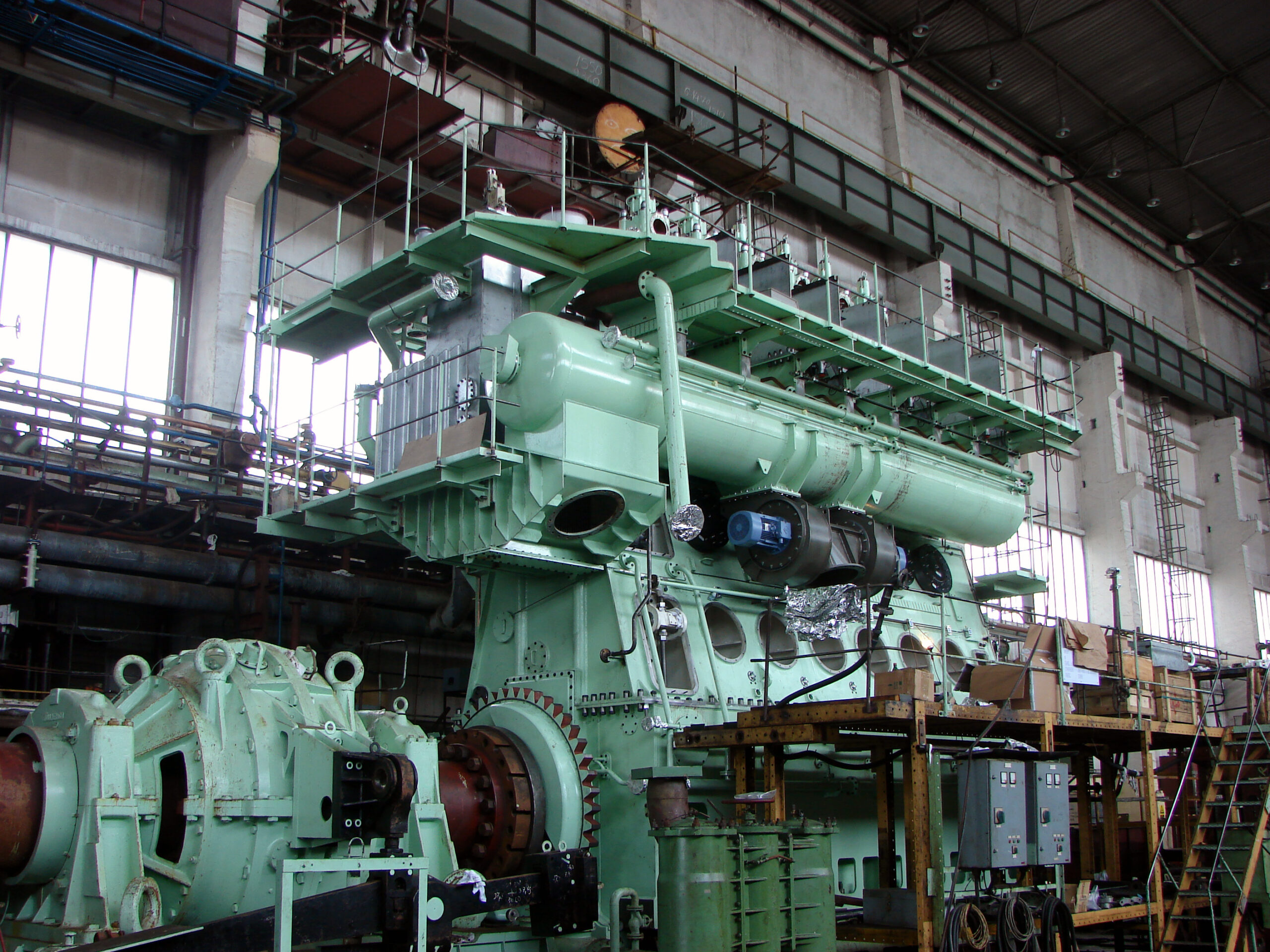
Initial Challenges
The plant faced significant wait times due to material handling delays and frequent machine downtimes. They had a disorganized layout, along with slow and un-optimized quality processes, which caused production bottlenecks.
Implemented Solutions
- Lean Manufacturing: The plant adopted the 5S methodology, which resulted in a cleaner and more organized workspace. Value stream mapping helped identify non-value-added activities, leading to their elimination.
- Optimized Layout: The introduction of cellular manufacturing reduced material handling time by 20%. A JIT production system was implemented, aligning production schedules more closely with demand.
- Automation: Automated guided vehicles (AGVs) were introduced for material transport, reducing manual handling time. CNC machines were used to automate precision tasks, increasing throughput.
- Workforce Training: Employees were cross-trained, enhancing flexibility and reducing delays caused by workforce shortages.
- Quality Control: Inline quality checks were implemented, catching defects early and reducing rework time by 15%.
- Supply Chain Management: Improved supplier collaboration and inventory management systems ensured timely delivery of components, reducing supply chain interruptions.
Results
The plant saw a 25% reduction in overall build times for engines. Machine downtime decreased by 30%, and productivity increased by 20%, demonstrating the effectiveness of the implemented strategies.
Conclusion
Reducing wait times in low volume manufacturing is achievable through a combination of lean manufacturing principles, advanced technologies, workforce training, robust quality control, and effective supply chain management. By addressing bottlenecks and optimizing processes, manufacturers can enhance operational efficiency, reduce costs, and deliver high-quality products more quickly to their customers.
Leave a Reply